01/16/2011 Frontken Ceramic Coating (Hot Build)
Thermal Spray Coating Rokide
The Rokide Spray System is a unique process utilizing ceramic oxide rods. The resulting ceramic-based coating provides excellent durability under extremely demanding conditions. Rokide coating is especially suited for applications requiring extreme dry abrasion wear resistance. Industries such as paper, petrochemical, oil, wire, and aviation/aerospace benefit tremendously from Rokide ceramic coatings.
In the Rokide process, ceramic rods are melted, atomized and sprayed at high velocity on the surface to be protected. Rokide forms an extremely hard, flexible and chemically inert coating that can be used as sprayed or finish-ground to a specified tolerance. This process requires no water, electrical power, or inert gases. Maintenance can be done in-house and does not normally require outside technical assistance.
Rokide rods are available in many ceramic oxide compositions, allowing our coatings engineers and customers to choose the most appropriate formulation for a specific application.
Advantages of the Rokide ceramic coatings:
Improved wear resistance
Ceramic coatings are much harder and much more resistant to wear and abrasion than metals. Ideal for pump components where sand, dirt, or other abrasive particles are present.
Improved heat resistance
Rokide coatings improve metal components with the protective properties of ceramic at temperatures up to 4500 0 F. Ideal for rocket engine exhausts and jet engine components; also appropriate for hot extrusion dies or components in contact with hot metal.
Superior electrical insulation
Ideal for parts used in electrical components. Can be used in wire-wound furnace cores and copper induction heating coils for both heat and electrical insulation.
Superior corrosion resistance
Ceramics are chemically inert, even in the presence of many corrosive chemicals, yet provide structural strength that other inert substances such as plastic lack. Rokide coatings are therefore ideal for chemical and process industry applications.
Reduced weight
In many applications, the total weight of the components in a process is a critical factor. Rokide contributes minimal weight to components yet provides superior protection and strength.
Material cost savings
Many Rokide coatings can give superior properties to relatively inexpensive materials. For example, a stainless steel pump body can be replaced by less expensive cast iron and coated internally with Rokide. Value engineering can uncover many opportunities to reduce operating costs.
Reconditioning of worn parts
The expense of replacing worn parts can be greatly reduced or even eliminated by reconditioning with Rokide coatings. Parts can often be reconditioned on location, saving the costs of removing, transporting and reinstalling.
Ceramic Chrome Oxide
Dense, corrosion resistant coatings recommended for resistance to wear by abrasive grains, hard surfaces, particle erosion and cavitation. Coatings are insoluble in acids, alkalis and alcohol. Some common applications are: pump seal areas, grounds, rolls and wear rings.
Coating Application Chart
Industry
Challenge
Component to be Coated
Plasma-Tec Solution
Pump
Resist cavitation
Resist hard surfaces
Copper alloy parts
Pump seals
Aluminum bronze
Chromium oxide
Performance Racing
Thermal barrier
Various
Yttrium Zirconia
Process
Thermal barrier
Resist molten iron
Resist molten zinc
Brazing/heat-treat fixture
Continuous casting mold
Galvanizing dip tanks
Zirconium oxide
Molybdenum
Tungsten
Machine Repair
Resist abrasion
Hard bearing surfaces
Salvage of steel parts
Grinder spindle seal area
Bearing journals
Various
Aluminum-titanium dioxide
Low carbon steel
Nickel chromium
Marine
Resist corrosion
Abrasive grain wear
Surfaces exposed to saltwater
Propeller shaft bearing
Pure aluminum
Titanium dioxide
Automotive
Resist fretting
Resist particle erosion
Resist corrosive gases
Oxidizing atmospheres
Differential ring gears
Exhaust valve seats
Piston heads
Exhaust mufflers
Molybdenum
Fused nickel-cobalt
Nickel chromium
Nickel chromium
Oil
Resist corrosion
Abrasive grain wear
Abrasive grain wear
Dump valve plug and seat
Sucker rod couplings
Slush pump piston rods
Fused nickel-chromium
Fused nickel-cobalt
Fused tungsten carbide
Printing
Abrasive grain wear
Resist abrasion/corrosion
Ink transfer rolls
Printing press cylinder
Aluminum-titanium dioxide
Stainless steel
Textile
Resist fiber and thread Thread guides
Rotor motor bearing fit
Loom motor rotor
White aluminum oxide
Nickel aluminide
Diesel Engines
Resist cavitation
Resist heat corrosion
Abrasive grain wear
Piston head
Cylinder liner
Fused nickel-chromium
316 stainless steel
High carbon-iron-molybdenum
Gage
Resist hard surfaces
Plug gages
Tungsten carbide
Electronics
Resist abrasion
Electrical conductivity
Dielectric coating
EMI/RFI shielding
Radio frequency shield
Magnetic tape heads
Electrical contacts
Heater tube insulation Electronic enclosures Instrument nuts
White aluminum oxide
Copper
Aluminum oxide-titanium
Zinc
Copper
Rotary Equipment Applications
Frontken services rotary equipment OEMs with an array of applications. Some of these applications include:
- Shafts
- Shaft sleeves
- Capstans
- Drawing dies
- Idler Pins
- Seals
- Plungers
- Crossheads
- Rotors and Rotor Shaft Assemblies
- Liners
- Cylinders
- Wear and Casing Rings
- Stuffing box
- Couplings
- Valves
- Hydraulic Cylinder Rods
- Pistons
- Spindles - Machine
- Glands, Seal
- Flywheels
- Pressure Plate
- Valve Rod
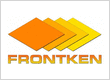
Dengan Hormat, PT. FRONTKEN INDONESIA adalah regional plant dari FRONTKEN CORPORATION BerhardPengalaman dan spesialisasi kami di bidang pengaplikasian Thermal Spray Coating dan optimasi kualitas coating untuk penggunaan di berbagai bidang industri yang spesifik dengan memanipulasi micro struktur dan…